The candidates in the 2016 U. S. Presidential Election often spoke of the connection between offshoring jobs and domestic unemployment. But restricting the domestic economy to "Made in America" goods is not as simple as it sounds, and comes with many consequences. The increasingly complex network of global trade has made "Made in America" an unsustainable luxury or superfluity for many - as well as an overly simplistic rallying cry for politicians.
Although millions of American jobs have been relocated to China and other foreign competitors, the desire to boycott imported products to bolster the market for domestic goods is complicated by America's current economic reality. Because incomes have improved so little since the Great Recession, many households are forced to seek out "the most convenient bargains" rather than products made in America. (Yet, some politicians argue that the benefit of reduced consumer prices is neutralized by the "layoffs and shuttered factories" resulting from offshoring.) American manufacturing employers "now seek workers with college degrees," thereby leaving the demographic of prospective workers with only high school degrees with few places to turn. There is also an increasing tendency for American companies with clients worldwide to view themselves as part of the global market - and in the process, creating complex and inextricable connections to non-domestic markets.
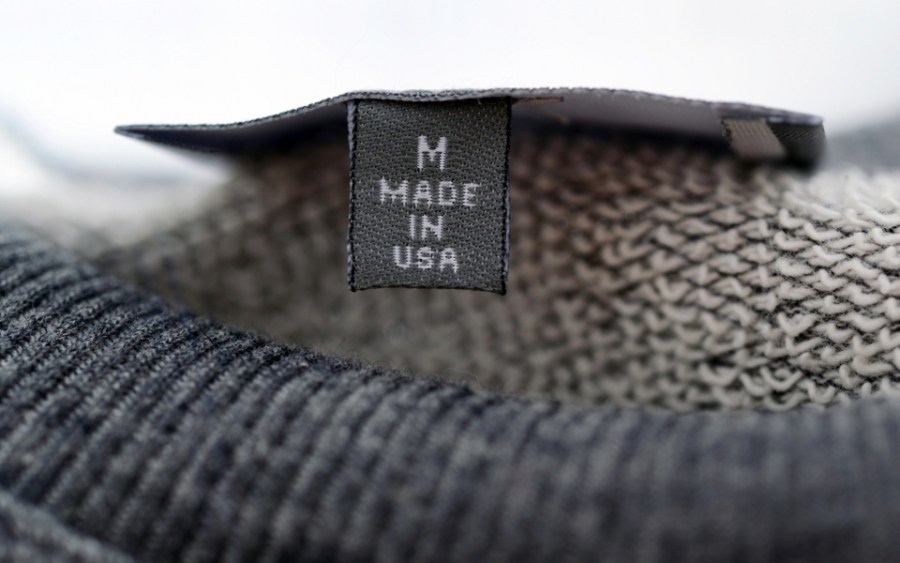
According to Mike Catherwood, a radio co-host for "Loveline," it is "definitely more expensive" to buy American-made products. As such, the "only people who can afford to buy them are the richest" Americans. On average, American households have a median income of "barely $50,000," according to 2011's Census. This bracket means they are able to shop at "stores like Walmart and Old Navy, emporiums of cheap imported goods" [NYSE: WMT and NYSE: GPS]. In a side-by-side comparison by the Huffington Post, the "classic 'Born in the USA' outfit" of "blue jeans, white T-shirt and work boots" costs over $421 if made domestically, but under $100 if imported from abroad. Mainstream, well-known companies that make their products in America include Red Wing, Levi's, American Apparel, J. Crew [NASDAQ: JCG] and Gilt Groupe. In contrast, their far-cheaper, outsourcing competitors include Brahma from Walmart, Hanes [NYSE: HBI], and the Gap.
It is a harsh reality that domestically produced goods are unaffordable for most Americans. However, this does not minimize the pervasive, American fear of offshoring jobs. Many Americans view importation as a source of diminishing American manufacturing jobs. But offshoring is precisely what keeps "the cost of living down for every American," making it possible for the "lower and middle class" to subsist comfortably in the present economic climate. Given this, the label "Made in America" (and even more local labels like "Made in Brooklyn") are presently gaining in social value, as it plays to wealthier consumers' desires to tap into the "locavorism" trend.
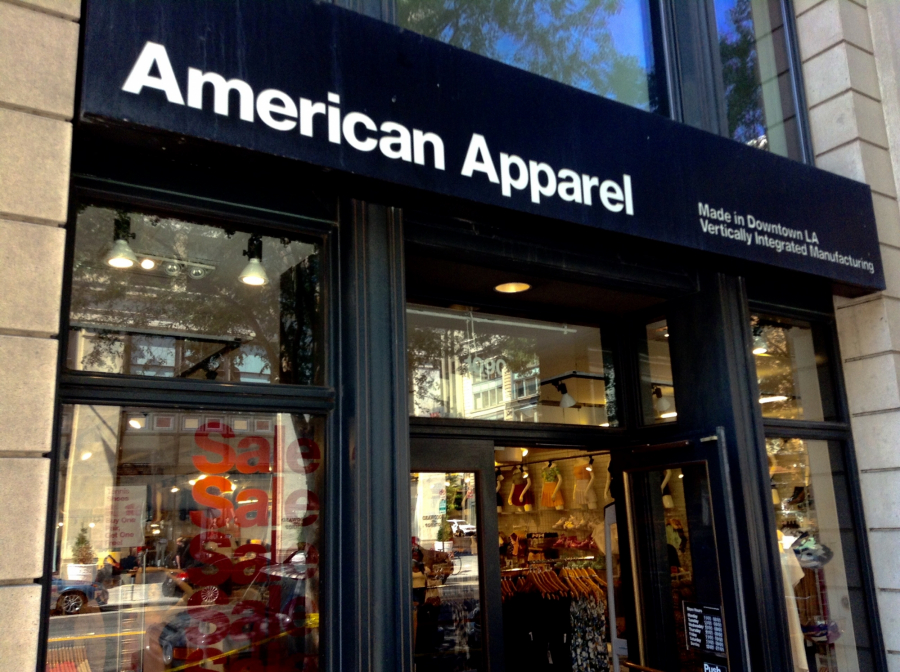
According to the Federal Trade Commission's regulations, a product can only qualify as "Made in USA" is "all or virtually all of the product" has been made in the United States. With the reality of globalized trade as a backdrop, this "distinction can get murky". America may import cotton, which is made into shirts overseas. Similarly, "Japanese cars are assembled in the United States". But sometimes this interconnectedness is not due to an economic choice that aims to maximize profit. America lacks many key domestic markets, and it resolves this problem by importing. According to a glib statement from Catherwood, "some things are impossible to buy" domestically, such as "electronics or...sex toys". Likewise, domestically produced condoms have been nonexistent since 2009, when the last condom manufacturer closed due to "tough price competition from the Chinese". This problem of absence applies to production infrastructure and workforce availability, as well. Outsourced goods are typically made in countries where companies experience no difficulties filling the appropriately massive quotas of workers required for certain factories to run, and certain goods to be made. One such example is iPhone manufacturing by Apple [NASDAQ: AAPL]. Estimates claim that the "Chinese workforce required to make the components and assemble the phones totals over 150,000". Meanwhile, no American factories of comparable size exist - and furthermore, a factory of those proportions would be unsustainable in context of the American factory-city landscape. A new kind of factory city would need to be developed, signalling that there is also a need for innovations in urban development, if America is to engage in direct competition with Chinese iPhone manufacturers, in this example. As of now, no American city is able to support a factory workforce of these proportions. To add insult to injury, "the infrastructure for these types of electronics was never in the US to begin with". In other words, "bringing back the jobs" to America would, in practice, require "building from scratch the entire manufacturing network that has grown in Asia over the last few decades". Rebuilding such an infrastructure in America would take unforetold amounts of time, and certainly dilute funding and efforts on America's part to reach the forefront of its various other domestic projects.
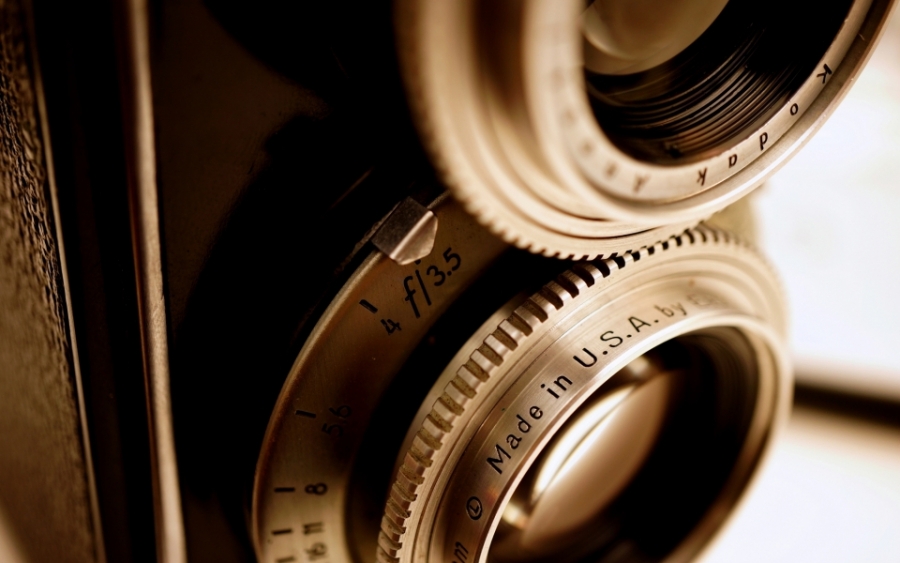
Labor rates in America are also much more expensive than labor rates overseas. On the cheaper end, the domestic labor rate is "$25-$30 per hour," a figure that "takes into account costs beyond an employee's wages". In contrast, in Vietnam and Bangladesh, costs are between $1 and $3 dollars an hour. This side-by-side comparison constitutes a difference of roughly $25 per shirt, if that shirt takes one hour to make. Despite this, due to efforts under the Obama Administration, many major companies have been "expanding their manufacturing operations stateside" since 2012. Some examples of companies that have done so include General Electric [NYSE: GE], Intel [NASDAQ: INTC], Canon [NYSE: CAJ], Caterpillar [NYSE: CAT], Apple and DuPont [NYSE: DD]. Their motivations for reshoring production often overlap with the unique difficulties that American companies can face overseas. Difficulties include the "lack of intellectual property protection for proprietary manufacturing processes, quality control issues, and the frustration of waiting weeks for products to arrive by container ship while rivals potentially rush hot new products to the shelves". The longer supply chain also creates more opportunity for exposure to "earthquakes and tsunamis, wars, oil shocks, and other unpredictable disruptions".
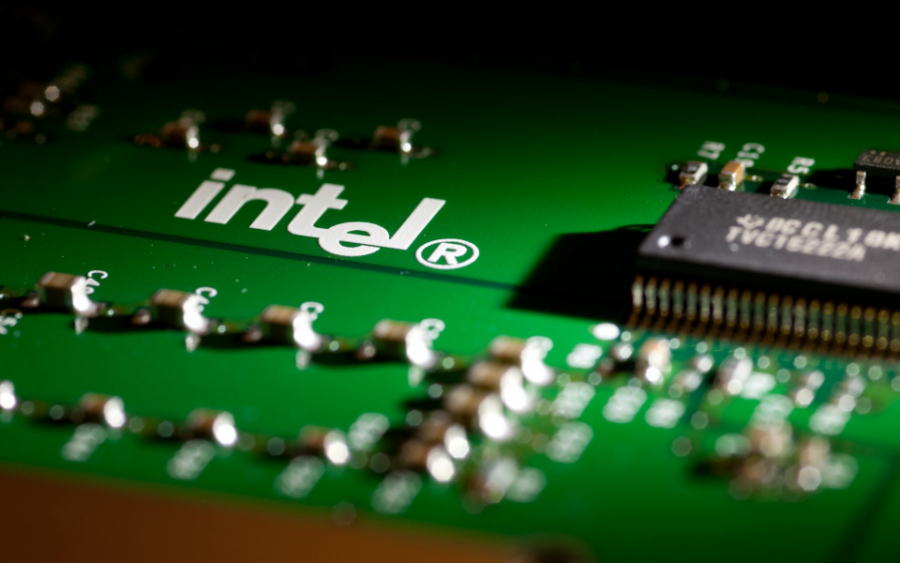
To actually create jobs in America, experts caution American manufacturers to refrain from separating production from innovation. Instead, they are urged to cultivate and improve upon existing, high-skill manufacturing initiatives. Increasingly, commentators observe that America's edge comes only through being able to answer, What can only America produce, competitively? To be able to answer this question head on, Americans must not continue to rely on "offshoring" as a comprehensive and rallying populist cry. Rather, Americans must accept that the recent decline in manufacturing employment is a global phenomenon - not a strictly American one. The existence of fewer manufacturing jobs in developed countries is a consequence of increasing gains in technology worldwide. Finally, mainstream American discourse must understand that certain, job-heavy areas of manufacturing will likely never return to America. These sub-sectors include "toys, apparel and home electronics". Hence, to bring more jobs to America, Americans should develop their nation's manufacturing infrastructure while focusing its efforts on the high-technology manufacturing sectors (e.g. the fields of solar technology and compact fluorescent lighting, to name two). In order to do so, America must develop its engineers and scientists - an effort that requires investment in a better education system and scientific research.
- 1. http://www.huffingtonpost.com/2012/09/17/made-in-america-the-luxury-label-will-cost-you_n_1891127.html
- 2. http://www.businessinsider.com/how-much-products-would-cost-if-made-in-us-2016-11/#jeans-2
- 3. http://www.chicagotribune.com/business/ct-americans-prices-vs-made-in-usa-20160414-story.html
- 4. http://www.nbcnews.com/id/35769753/ns/business-us_business/t/yes-we-do-still-make-things-america/#.WNbP5hLytE4